DIY & Home Improvement
Related: About this forumQuestion about AC motor brushes
Is there a reason that the copper wire connecting the carbon brush is not insulated?
I've just been learning about these motors while trying to fix some household devices, and one thing I've noticed is that *all* the other wires are either coated or sheathed, *except* the short (~1" ) wire connected to the carbon brush.
I'm about to reassemble one, but suddenly wondered whether I should insulate those wires first.
Does it have to do with flexibility so that the brushes are minimally restricted?
It just seems like such a vulnerability.
If anyone knows, please advise asap. TIA!

SheltieLover
(59,605 posts)Also could be part of wire near brush not having anything to short out against.
Flex is likely a part of the reason though.
intrepidity
(7,891 posts)I guess I was concerned about moisture/water, but now that I'm looking at the housing, every part within reach of that wire is plastic (lol, doh!) so even if it got wet, no matter (right?).
Learning is fun!
SheltieLover
(59,605 posts)From my genius grandson who adamantly agrees that learning is fun!
He is always happy fo dictate answers to questions about car repairs, hvac, electrical stuff & computers.
intrepidity
(7,891 posts)(heheh, kidding) although I wish he were my neighbor!
Thanks again, and to your lovely grandson.
Yonnie3
(18,111 posts)I've never seen an insulated brush wire. I think that it is so the brushes can move freely. The brushes and their wire can get hot so ordinary insulation wouldn't be OK. Those that I worked on had plenty of clearance around that wire and it was a special braided with very fine gauge strands. I would caution that replacement brush's wires should be the same length as the original.
intrepidity
(7,891 posts)I'm reinstalling the originals, but good to know for future (now that I'm becoming an "expert" (lol) on these things, I imagine I'll be tearing down every household item soon....) Right now it's shop vacs. Next up: food processor.
RKP5637
(67,112 posts)exactly the correct brushes. If installed correctly the clearance is more than adequate.
intrepidity
(7,891 posts)As noted above, I just noticed how everything within reach of that wire is plastic...
intrepidity
(7,891 posts)I notice the armiture and housing are prone to rusting. I'm pretty sure I can gently sand that off (is 150 grit too coarse?), and I understand that I must meticulously brush/vac/blow any debris out after, so no metal particles lodge in an unfortunate spot. But can I apply WD40 to those pieces carefully before reassembly?
I will soon know whether it's ok to submerge the whole thing in Evaporust--well, technically it surely works well at removing all the rust--it remains to be seen whether the motor will still function.... I've tested continuity between all pieces (adjacent commutator bars; diagonal bars; bars to armiture; any more?) and everything seems ok.
I've been intimidated by motors my whole life, so this is an adventure.
RKP5637
(67,112 posts)destroy plastic, etc. It really damages cars too when people spray it around in the engine compartment. It's best to leave as much as you can alone. Just blow out carefully any dust from the brush area, etc. and do not apply chemicals to it. I would back off on any sanding. I would also back off on doing much to the commutator. If it's severely worn it might need turning on a lathe in a motor shop. I hope I reached you in time.
intrepidity
(7,891 posts)I already did virtually everything wrong on this one, though.
Although, I did reinstall it finally last night, and it works. But, being an idiot, I forgot to put the filter back on (shop vac) before using it, so now I have to completely disassemble again to blow out any new dust :sigh: Sometimes I think I'm just not cut out for this, yet I enjoy it and continue doing it.
Thanks for your help.


KY_EnviroGuy
(14,595 posts)Do not sand on a motor armature or stator laminations because they're made of laminated steel sheet that are insulated like a transformer core. Just brush the loose stuff off (a stiff plastic brush like an old denture brush would be good).
You can protect most motor parts from further rusting by spray or brush coating (very thin) with clear acrylic paint and dry it well in a low-temp oven or under a heat lamp. Bake until you no longer smell solvent and the coating is hard. Be sure to not spray the brush commutator and bearings. High-temperature varnish is normally used for motors. WD-40 on a motor could cause a fire and it would be a dirt magnet.
But most importantly, do not submerge motor armatures or stator windings in anything. Nothing should be used (including coatings) that will leave residues that could inhibit air flow around the windings. It can be done but requires special cleaning solutions and a drying oven.
For other rust prevention, cleaning and lubricating purposes, products like Boeshield (Boeing Corp.), B'laster (The B'laster Corp.) and Industrial PCL (San/Bar Corp.) are far superior to WD-40.
You could learn a lot by visiting an old-fashioned motor rebuild/rewind shop.
KY
RKP5637
(67,112 posts)intrepidity
(7,891 posts)If the armiture and stator are laminated, why does the rust form?
Anyway, too late for this one; I already had completely submerged it in Evaporust (does excellent job of rust removal!) then used a steam cleaner, then air compressor and several days of drying.
Then I did sand some surfaces lightly, and applied (with a cloth) a light coat of wd40 (avoiding any plastic or wires or anywhere near commutator).
One of the bearings was a bronze sleeve, and I applied some drops of a PTFE lube into the cushioning.
Reassembled, and it works, so there's that. For now.
Next time I will heed your suggestions, thanks very much. I especially like the paint idea -- when you say high temp varnish, do you mean the clear acrylic? Is there a high temp clear spray paint? I've never seen one.
ETA: say, could I use clear nail polish on those parts?
KY_EnviroGuy
(14,595 posts)Armature and stator steel laminations only have a very thin coating of varnish that is not perfect. Therefore, pinholes in the coating would allow moisture to enter and rust, like cancer tends to spread. Many motors are subjected to temperature extremes and hence subjected to condensation.
Clear nail polish is excellent for coating electrical connections to block moisture but not suitable for high temperatures.
It's far better to use electrical varnish on motor internals than acrylics due to temperature ratings. Acrylic would probably be OK for the exterior of a motor housing and you can find that at hardware stores.
Typical small cans of brush-on e-varnish:
https://www.eis-inc.com/catalog/varnish-resins-and-coatings/varnishes/varnish-ph21-synthite-ac-46?option=varnish-dolac46
General listing page: https://www.eis-inc.com/catalog/varnish-resins-and-coatings
or...https://www.alliedelec.com/product/mg-chemicals/4226a-55ml/73641102/
Spray-on e-varnish: https://www.mcmaster.com/7437K21/
E-varnish Properties (from McMaster-Carr):
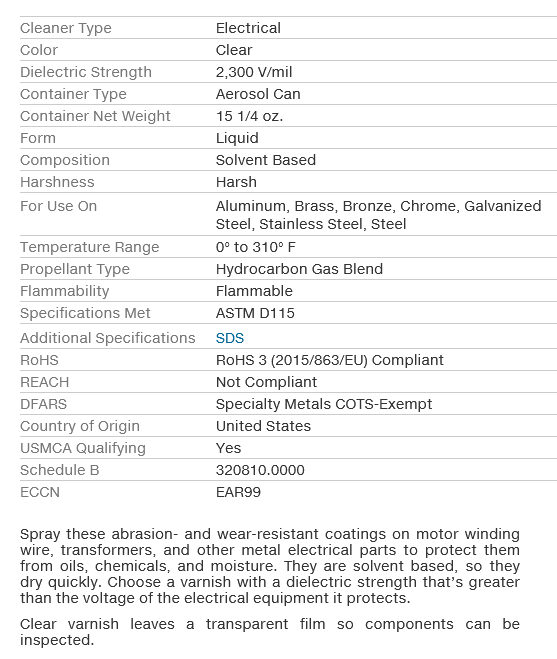
Now, compare the temperature ratings of this acrylic product: https://www.mcmaster.com/7850T4/
Properties:
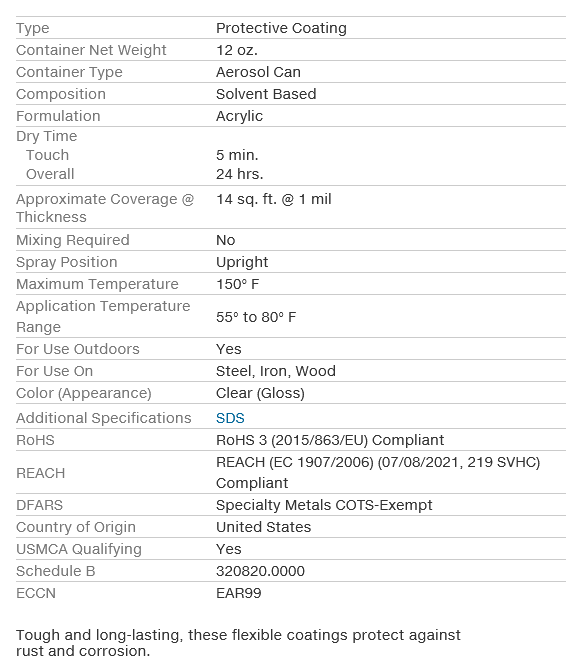
This product might work as well but I don't know the thermal properties: https://www.lowes.com/pd/Natural-Earth-Paint-Natural-Varnish-4-oz/5005463737
As you can see, the proper product to use can be quite expensive. If you have a local motor shop, they would probably give you a small quantity if you bring a safe container, consider they probably buy it in large drums for their motor dipping tanks.
Hope this helps and it gave me a refresher on a few topics!......

KY
tech3149
(4,452 posts)The brush needs to ride the commutator as tightly as possible. That's also the reason there are a bunch of small gauge wires braided together. If you put an insulator around them it would restrict the movement. There shouldn't be anything in the area of those shunt wires for them to short against.