Science
Related: About this forumTechnoeconomic Assessment of BAAM for NdFeB Magnets (Additive Manufacture vs. Molding.)
The paper to which I will briefly refer is this one: Comparative Techno-economic Assessment of NdFeB Bonded Magnet Production: Injection Molding versus Big-Area Additive Manufacturing Xiaoyu Zhou, Mariappan Parans Paranthaman, and John W. Sutherland ACS Sustainable Chemistry & Engineering 2023 11 (36), 13274-13281
As the title of the paper makes clear, BAAM is "Big Area Additive Manufacturing." This is a big area of research at Oak Ridge National Laboratory. They have demonstrated printing nuclear reactor cores there.
Although Oak Ridge is a center for the development of nuclear technologies the paper begins with text including an adjective phrase I find dubious, which includes (as bolded by me) statements about wind turbines and electric cars being effective approaches to doing away with fossil fuels.
To wit:
Given the supply risk associated with rare earth elements and associated price volatility, a number of strategies are being pursued globally to limit the risk, e.g., finding new sources for these critical materials and developing material alternatives. One strategy that seems to offer promise with respect to REPMs is to recover magnets from end-of-life (EOL) products and capture magnet waste during sintered magnet processing. It is envisioned that such reclaimed materials could be used to fashion new magnets and, thus, temper the demand for virgin resources. A comparative life cycle assessment of producing magnets from virgin materials and through magnet-to-magnet recycling showed that recycling is an environmentally preferable choice. (9) Furthermore, recycling is also preferred with respect to magnet performance since it enables the adaptation to newly discovered methods that improve magnet strength and ductility. (10)
I have also high lighted the word dysprosium, which I discussed in this space recently: Unlocking Dysprosium Constraints for China's 1.5 C Climate Target
Even in China, which dominates the world supply of lanthanides, there isn't believed to be enough dysprosium to build all these bat and bird chopping wind turbine industrial parks that are supposed to save the world, but haven't done so, aren't doing so, and I contend, because of their lack of sustainability, won't do so.
Still we chant on.
Electricity is a thermodynamically degraded form of energy, but within limits well below all the associated fantasies about its sources (which are dominated by dangerous fossil fuels), electricity is a very valuable form of energy, as any fool, even me, can see. In modern times its generation is dominated by NdFeB magnets. The constraints of the supply of these make it extremely dubious to put them in wind turbines, since the materials in a wind turbine are all stranded assets when the wind isn't blowing, but no matter. It follows that the best use of limited resources is in reliable clean systems with high capacity utilization, that is in nuclear plants.
It takes a lot of energy to make these magnets, some of which is heat energy.
Some additional text from the paper:
...
A bonded magnet contains a mixture of magnetic powder and nonmagnetic polymer or rubber binder. (17) There are four methods to manufacture bonded magnets: compression bonding, injection molding, extrusion, and calendaring. The end products of compression and injection molding are rigid magnets, which provide good magnetic performance and are not excessively brittle; these processes are generally economically competitive. Calendaring can produce only flexible magnets. Both flexible and rigid magnets can be produced using extrusion...
...Manufacturing magnets through compression bonding starts with melt spinning, which melts NdFeB ingots. The molten alloy is poured into a tundish and directed onto the surface of a quench rim to form a ribbon through the nozzle at the bottom of the tundish. To get a finer grade of the powder (less than150 ?m), the ribbon is crushed and annealed in an inert atmosphere. Then, the crushed powder is encapsulated or blended with the bonding resin. After that, the epoxy encapsulated powder is compacted into a green compact of the desired shape...
Getting to the point, BAAM:
A table comparing the mass and energy intensity of two processes for magnet manufacture, injection molding and BAAM:
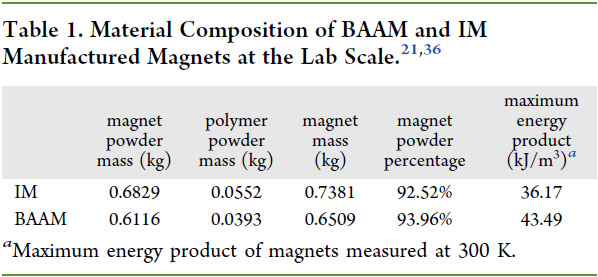
Another table and picture from the text:
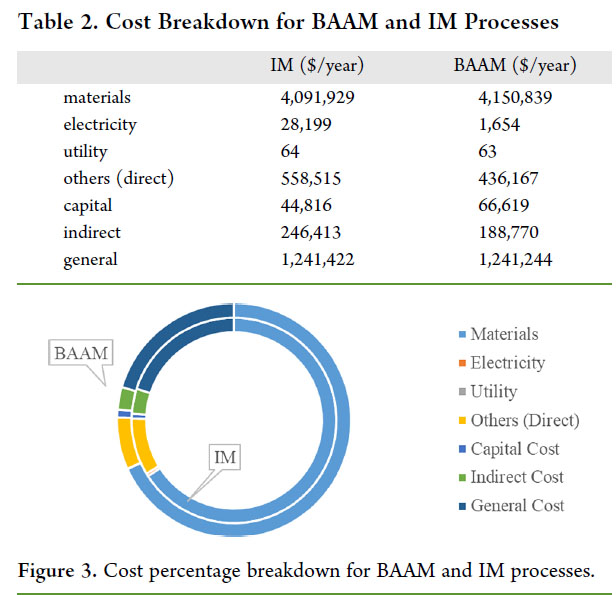
The profitability is a function of scale, apparently, with BAAM scales being slightly less profitable than injection molding on current scales but in terms of energy consumption and material costs, BAAM is superior and cleaner and may ultimately be more profitable.
The authors conclude:
I trust you're enjoying the weekend.